IQF Tunnel
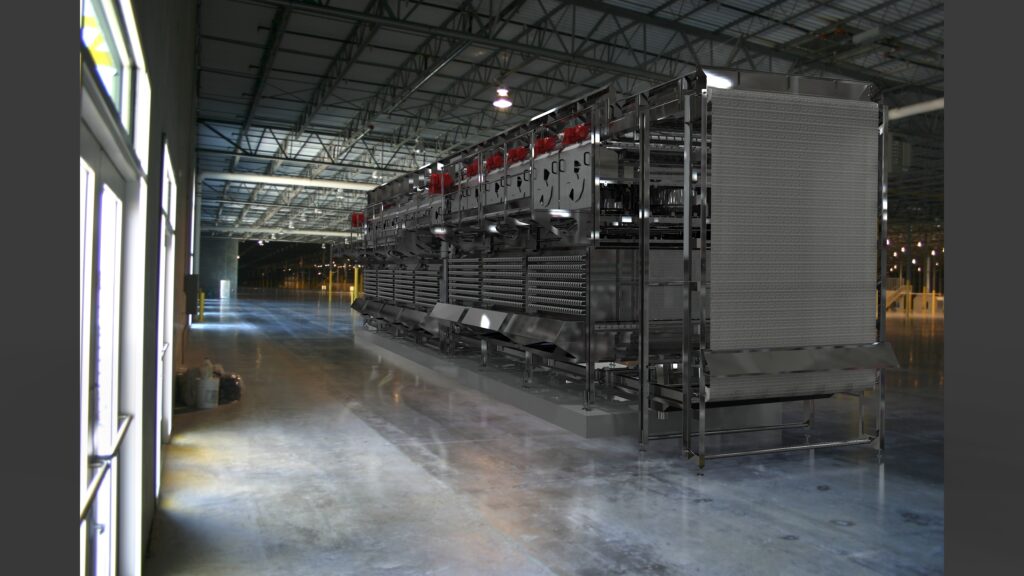
AFE created one of the world’s largest freezing tunnels.
Leading meat processors rely on our IQF (Belt) freezers for safe and dependable food processing. Manufactured with stainless steel, IQF tunnel freezers are safe and worry-free food-processing freezers that offer ease in cleaning and unsurpassed reliability.
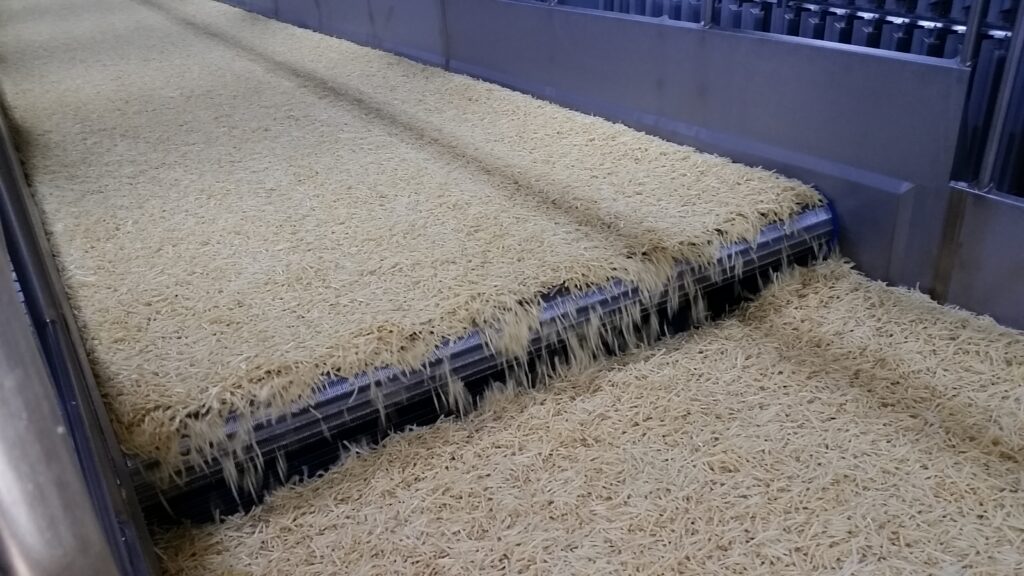
IQF tunnel freezers are cascade, inline positive-conveying freezers that circulate cold air through your food products. The freezers are engineered and built for your production needs.
Through the IQF tunnel, excess surface water is removed, and cold air is recirculated using a pre-cool zone, where moisture is sealed in and product is separated. A core freezing zone uses continuous fluidized agitation to remove product core and latent heat.
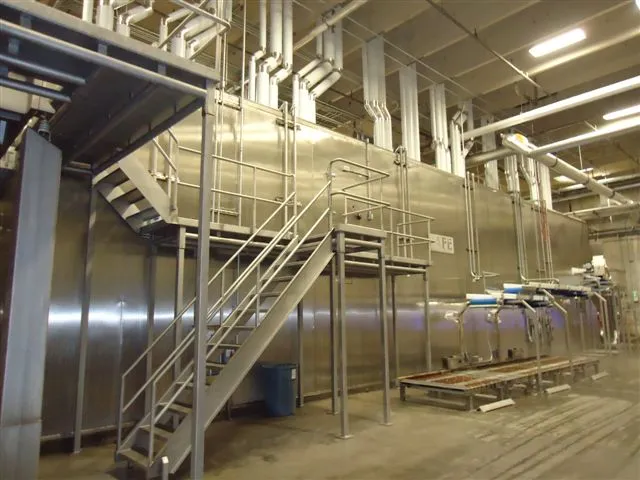
Benefits of AFE IQF Tunnel Freezers:
- Excellent freezing quality
- Reduced product shrinkage
- Coil is shielded from contamination
- High pressure washer system
- Modular design allows for future expansion
AFE’s IQF Tunnel Freezers have been provided since 1990. AFE IQF Tunnel provide the ideal freezing process, whether processing heavier food products like broccoli or mango or processing lighter food product like raspberries. We can custom manufacture your IQF Tunnel Freezers to suit the water content, weight, shape, and fragility specifications of your food products.
LARGE CONTINUOUS OPERATION VEGETABLE FREEZERS
- Continuous operation for a day or days without stopping
- High production, built to meet your production needs.
- Full sequential defrost for multi-week runs
- Reliable
- SS welded or SS clad panels
- Can be used for all vegetables including leafy herbs and spinach
PACKAGED FREEZERS FOR MEATS AND VEGETABLES
- Modular and installs in days
- Air defrost or sequential defrost
- Drive motors external to freezer
- Welded stainless steel enclosure
- Particle and chunk products
- Common capacities over 20,000 pounds/hr
CONTACT BELT TUNNELS
- Modular or site built
- Extended run or sequential defrost
- Welded SS steel or SS clad enclosure
- Common capacities over 20,000 pounds/hr
- Can be used for wet, sticky products or liquid products
- Virtually no belt marks
DRAG TUNNELS
- Modular or site built
- Extended run or sequential defrost
- Welded SS steel or galvanized floor
- Designed to meet production needs
- Products loaded in carts
- 1-6 Lanes with separate retention times possible
EVAPORATORS
- Stainless steel tube
- Straight or staggered tube pattern
- Wide fin spacing
- Aluminum magnesium fins
- Various configurations available
- Sequential defrost for continuous operation
- Air defrost to double run time
- Extended run time coil design
WELDED ENCLOSURE
10-Year Warranty with leg supported floor system, the best warranty in the industry
Provided since 1990 and associated design experience.
CLEANING SYSTEM
Full foam cleaning system with zone control and strategically placed rotating nozzles. Single pass or recycle system. Steam pasteurization is available with a welded enclosure. Easy to clean and hygiene friendly. Continuous seam welding method seals each freezer to prevent bacteria growth and ease of sanitization.